As a world leader in testing, inspection and certification, Bureau Veritas has been in business for 180 years, with 80,000 employees in 160 countries. Their mission is to support their 400,000 clients in managing risks related to quality, safety, health and social responsibility.
Bureau Veritas is one of SENAR’s oldest customers, and is particularly experienced in the use of Augmented Reality on mobile devices, having trained more than 2,000 of their clients' employees on our simulators. Below, we interview Guillaume Laurent, Director of Training France to see how Bureau Veritas has benefited from using SENAR.
Where does Bureau Veritas' interest in mobile AR come from?
Innovation is in our DNA at Bureau Veritas. From our inspections, to certifications and training, we've been innovating for 180 years. For example, we rolled out inspections using Google Glass, and inspections that use drones. It was a natural next step for us to look at immersive technologies and their potential benefits for our customers. We saw it as a way to further improve team training on safety procedures. And we quickly realized that mobile AR was the technology that would check all the boxes.
What boxes were you looking to check off?
Our requirements were quite simple: we wanted a solution that would be of real educational interest while also being hands-on. It had to be fun and ergonomic to ensure all the people involved would want to use it. But above all, it had to be scalable: instructors would need to be able to implement it very easily, without trainees having to learn how to use the device or the app before starting their training.
That's where things got stuck with Augmented Reality's rival technology, Virtual Reality. There is nothing immediate about getting used to a VR app. You have to start by training each instructor, then each trainee, to use the headset. You also need 2 to 3 times as many instructors for each session. Some users are resistant to VR headsets or do not tolerate them well (problems when wearing glasses, nausea, headaches, etc.). It would have been much too complex for us to deploy the project on a fleet of VR headsets, not to mention the substantial difference in cost.
So we quickly decided on mobile AR and a fleet of iPads, which removed all these obstacles.
How did your experience with mobile AR start?
We started by testing it on our electrical clearance training courses. In France, the labor code requires all employers to train and authorize personnel working in proximity to electrical equipment. The subject was particularly well suited to AR and the demand was there: our trainees and instructors had been asking us for training courses that were more hands-on and less theoretical for a long time. The simple answer was to say, "OK, let's install training workbenches and cabinets everywhere." But that was complicated to set up, and very expensive in terms of manpower and materials.
After deciding in favor of mobile AR, we did a Proof of Concept with SENAR in early 2019. Then we went into Lab mode to develop the exercise scenarios. Production was launched in September 2019, with a first training center, before expanding the experiment to 12 of our centers. Today, we have deployed SENAR throughout France.
What does an AR simulator actually look like?
It generally includes a list of several scenarios. The flow of each of them is very similar to a real-life procedure, while being very "gamified".
When trainees launch an exercise, they first learn about their mission. It is very concrete. For example, they will be asked to perform the lock-out/tag-out process on electrical equipment before changing the blades of an industrial mixer. They start by choosing their PPE, equipment and markings on a virtual shelf. Depending on the level of difficulty, they may or may not be shown the number of pieces of equipment they need to select.
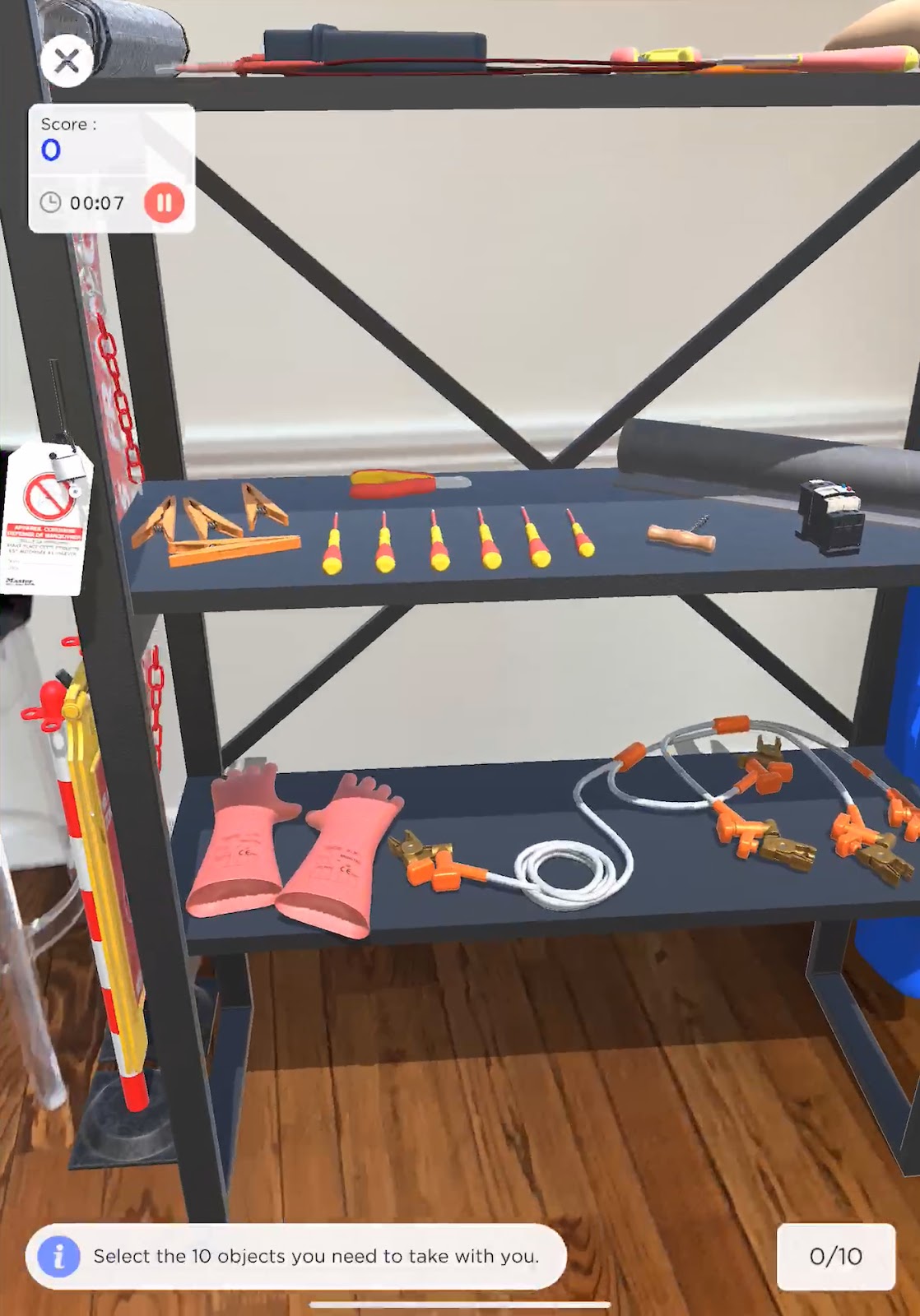
The trainees will then check their equipment. Without leaving the simulator, we can then ensure their level of understanding with more traditional methods: having them answer a multiple choice question, showing them a video of a precise technical skill. Then the learners are invited to perform all the tasks in the procedure, one after the other, on a virtual and interactive electrical cabinet.
Before opening the cabinet, the trainees see the insulation mat unrolling on the floor, and the markings they have chosen appear in place. When they open the cabinet, they can hear the real sound of the door. As in a real electrical cabinet, they have to consult the wiring diagram to identify the components they will be working on. Down to the last detail, everything is identical to the physical cabinet they will later have to work on to pass their test.
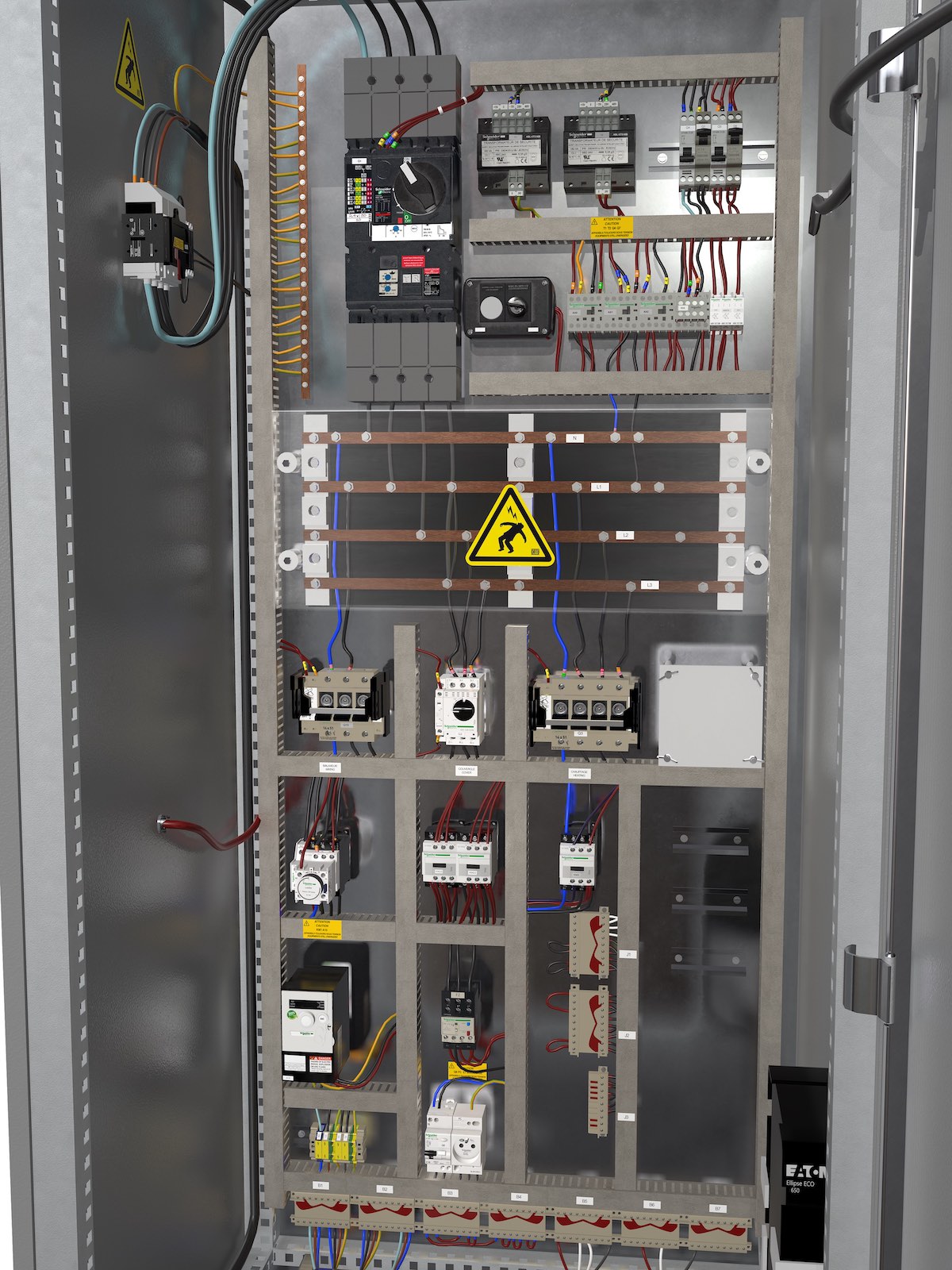
What about reproducing accidents, which is often mentioned as one of the strengths of AR?
This is indeed a key point! In the simulator we use for our preparatory training courses for electrical clearance, a key component consists of identifying the work area and carrying out a risk analysis. If this analysis is done incorrectly, the trainee is still able to continue the procedure. But a little further along in the scenario, an accident will suddenly occur, such as an arc flash, or an attack by a swarm of wasps nesting in the cabinet. The fact that the accident happens by surprise - exactly like in real life - is the best way to make the learners more vigilant in their future risk analyses. They learn and progress from their mistakes.
The great advantage of working with SENAR is that they have recreated our own accidents, based on historic experience from our teams in the field. The wasp nest, for example, is not a risk that trainees would necessarily think about, but it happens! The inside of an electrical cabinet is hot and dark; insects love it.
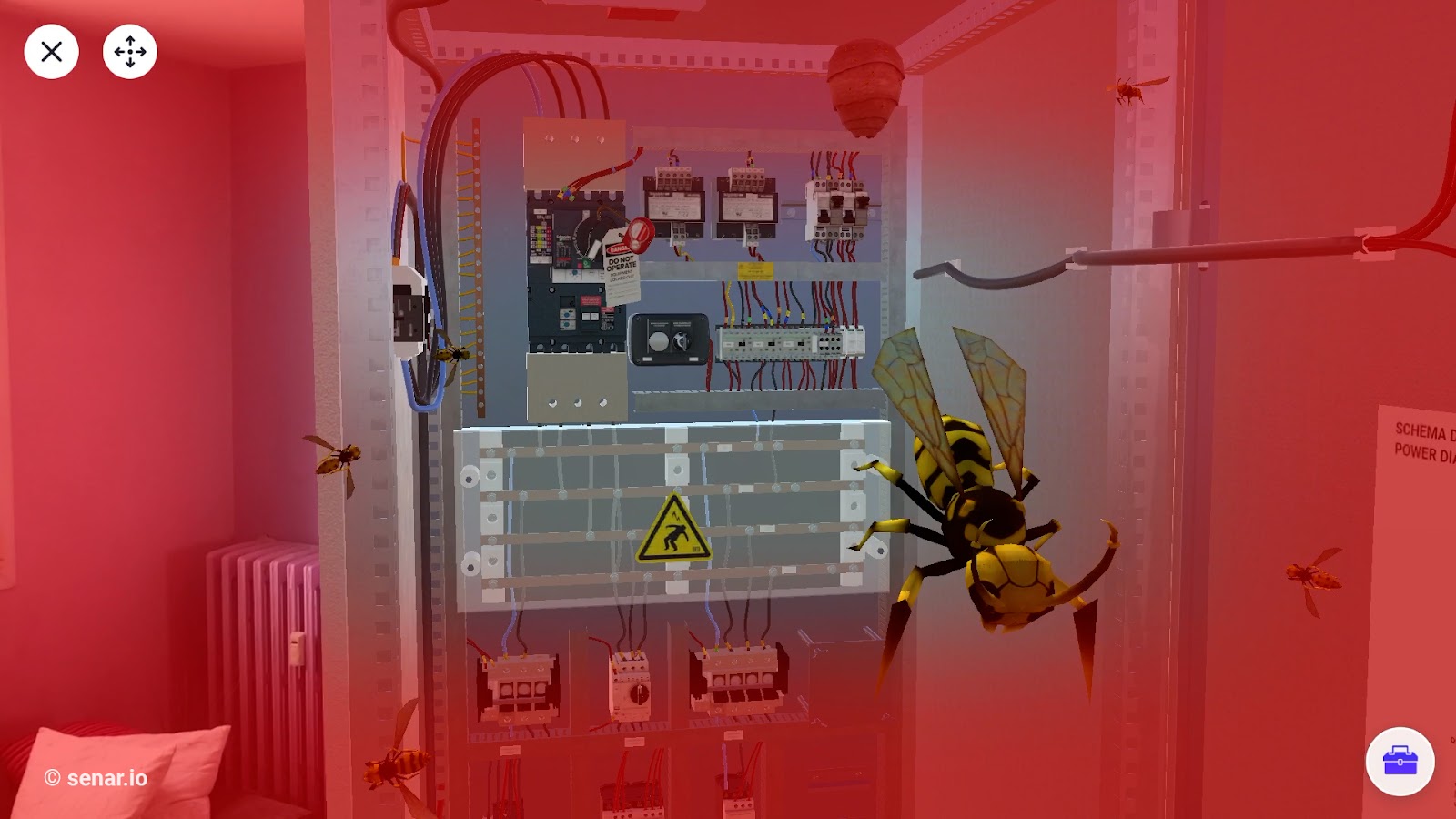
What do you see as the main advantage of mobile AR training?
The key advantage of AR simulators is that you can practice and repeat exercises over and over again. Of course, we wanted our scenarios to be practiced repeatedly, because we know that the adult brain memorizes much better by practicing and repeating. But the trainees went beyond our expectations by really getting into the game. Gamification and point logic have the huge advantage of encouraging learners to retry a scenario even if they did well overall on the first try. They make it a personal challenge to earn more points and to outperform their colleagues nearby!
The direct result is that key safety skills, such as risk analysis, are repeated over and over again. This is one thing that really struck us: on their first try, some trainees will botch their risk analysis in 5 seconds. An accident will then take them by surprise. On their second try, the risk analysis will take 25 seconds. On the third try, we saw trainees go around the cabinet three times, and even lie down on the floor to make sure they didn't miss any anomalies!
What other advantages do you find most appealing about mobile AR?
I think it would be that AR makes our training sessions more dynamic. First of all, as we just mentioned, during an AR training session, the group competition plays an important role. It is motivating for everyone. But also, in real hands-on training in electrical clearance, for example, an instructor cannot supervise more than 2 or 3 trainees, primarily for safety reasons. Now, instead of spending part of their training time reading documents or completing quizzes, the other trainees can practice on the AR simulator. As a result, they are already highly trained when they come to the electrical cabinet for real hands-on practice.
The feedback from instructors is also very positive. They feel freed from the confines of a PowerPoint presentation. Less talk, more action!
You also mentioned an ecological advantage...
Yes, that's a pretty nice bonus: using an AR simulator is also good for the environment. The impact on our carbon footprint is significant in terms of equipment installation and travel.
During a fire safety training course, you can practice the exercise over and over again without using consumables such as gas for the fire tank or refills for educational extinguishers. In AR, there is no waste and no garbage to be thrown away.
How do trainees respond to this new training method?
To date, more than 2,000 people have used our AR simulators in a training session. As a result, we have quite a bit of hindsight, and a lot of feedback from our learners. The first thing they love is the fact that they can see a virtual object in their real, everyday environment. It is certainly simpler and less intimidating for them than a VR headset would be.
In terms of feel, the simulator replicates about 80% of the sensations encountered in real life. What is missing are the sensations of pressure, tightness, or temperature. Trainees mention things like feeling the weight of a screwdriver in their hand, or the resistance of a screw, for example. That is very complicated to reproduce in AR. Apart from that, they consider the experience very realistic. The immersion effect created by the sounds is also a point they mention quite often, because it contributes to making it a full experience.
Our trainees and instructors also appreciate having several scenarios to play. Some trainees have told us that they have been training in electrical risk for many years* and have never had the opportunity to practice so much, in such varied scenarios.
* Note: The French National Research and Safety Institute for the Prevention of Occupational Accidents and Diseases (INRS) recommends that an employee's electrical clearance be renewed every two years, with each renewal leading to refresher training.
The Data
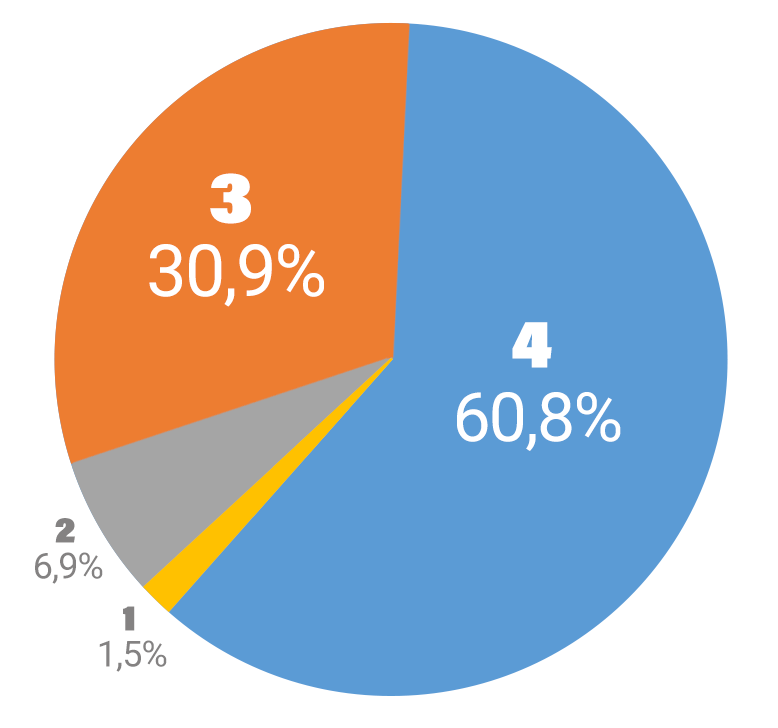
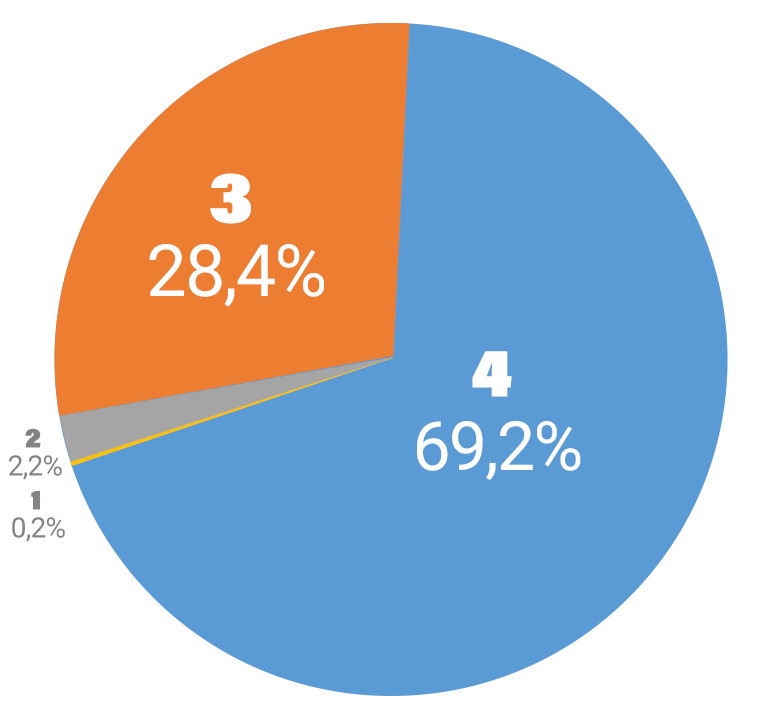
Note: These evaluations are based on a survey of 205 trainees conducted between September 6 and October 20, 2022
Is mobile AR immersive enough for professional training?
Without a doubt. AR reaches a level of realism that is really amazing. When the trainees carry out a no-voltage check on the AR simulator that we use for preparatory training for electrical clearance, between the animations responding to their interactions, the sound of the tester and the probes entering the terminal blocks, we see them focused and fully immersed in the experience.
In the fire safety simulator, there is smoke, flying particles, cracking noises, etc. You can even get burned (virtually) if you get too close. The shrill sound of the alarm adds to the trainee's stress, projecting them with even more realism into an emergency situation. Every detail can be observed up close; for example, you can look at the charred remains of a garbage can and identify the waste that caused the fire. And then, if the user is slow to react, the fire spreads beyond the trash can. It is particularly striking to experience the consequences of one's actions, or inaction. Especially when you see the flames start to invade the training room!
Another advantage of AR is that only the equipment that is useful for the scenario is represented; the learner is not distracted by a virtual environment which would tempt some people to hunt for “errors” by examining the color of the virtual flower pots!
What about training in AR, in terms of regulatory compliance and labor laws?
For fire safety, the labor code requires that each employee is trained in the use of a fire extinguisher and in recognizing the alarm sound. Obviously AR is not real hands-on training, but it is very good supplemental training. It's a cross between the theoretical and the hands-on part of the exercise.
What insight do BV instructors have into what their trainees are doing in AR?
The instructors have access to an online reporting console that is an integral part of the SENAR platform. There, they can see the results, successes and mistakes of each trainee, at each stage of a scenario. They can, for example, see if several trainees have "stumbled" in the same place and immediately rectify the situation by re-explaining a point that was misunderstood. In a hands-on classroom, no matter how large, it is very complicated to manage 10 learners in 10 different teaching facilities, if those facilities exist in the first place. With AR, this becomes possible.
How long did it take your instructors to be trained on the SENAR platform?
Our instructors involved in electrical clearance were trained in half a day. We presented them with the pedagogical sequencing and the SENAR platform (mobile application, reporting console) for just over an hour. They then spent 2 hours repeating the exercises in AR, on iPads. The learning curve is very fast.
How is Bureau Veritas' AR training delivered?
Today, mobile AR is a teaching tool that instructors integrate into their training sessions.
And because it offers the flexibility of being very scalable, we have also started to use it in virtual classes. All the learner needs is a tablet or smartphone compatible with augmented reality, which is the case for 80% of all mobile devices less than 5 years old. You don’t even need an especially good network connection, as the internet is only needed during the time it takes to download the application and simulator, which is only one or two minutes. Once the simulator is installed on the mobile device, no internet connection is necessary to play - oops! - I mean, to practice. And the trainees can continue to practice after the training session if they wish.
Even in the classroom, several students wanted to run SENAR on their smartphones instead of using the iPads provided in our centers. These trainees preferred to remain on familiar ground and not have to integrate the use of an iPad. This is the solution we are advocating for today to make AR adoption even easier. In the end, we learn from our learners too!
Which of your training courses include mobile AR?
We use SENAR AR simulators during our training courses on electrical clearance and fire safety. We have also deployed simulators for the inspection of harnesses and slings during Safety Days at our customers' sites, and we will soon be integrating them into our catalog training courses.
First Aid simulators will also soon find their place in our training courses, for our customers who want an alternative to "First Aid at Work" training.
Finally, we are integrating customized simulators to meet the specific needs of certain customers, in particular for LOTO (Lock-out/Tag-out) procedures.